Air blasters play a crucial role in the cement manufacturing process. These devices are designed to remove material build-up or blockages in various equipment used in the cement production line. The cement manufacturing process involves the handling of raw materials, such as limestone, clay, and iron ore, which are then crushed, ground, and mixed to form the final product. Throughout this process, material can accumulate and cause blockages or build-up in equipment such as silos, hoppers, chutes, and kilns. This is where air blasters come into play.
Air blasters use high-pressure air to dislodge and remove accumulated material from the equipment. They work by releasing a blast of compressed air into the blocked area, effectively breaking up the material and allowing it to flow freely again. This helps to maintain a continuous and efficient production process. Without air blasters, equipment blockages can lead to costly downtime, decreased productivity, and potential damage to the equipment itself.
Furthermore, air blasters contribute to energy efficiency in cement manufacturing. When material accumulates in equipment, it can impede the flow of air or gases required for certain processes, such as combustion in kilns. By removing blockages with air blasters, the flow of air or gases is restored, ensuring optimal energy usage and reducing fuel consumption.
Overall, air blasters are essential tools in the cement manufacturing industry. They help prevent blockages, improve safety, and promote energy efficiency. Therefore, investing in reliable and efficient air blasters is crucial for cement manufacturers to ensure smooth operations and maximize productivity.
Increased Profits: Maintaining optimal material flow leads to higher revenues and greater profitability.
Enhanced Efficiency: Eliminating blockages and build-up significantly boosts throughput without substantial increases in labour or energy costs.
Improved Safety: Workers no longer need to manually address blockages inside containers or beneath unloading ports, promoting safer working conditions.
Equipment Preservation: Unlike manual cleaning tools that can damage equipment, air cannons use harmless bursts of air, minimizing wear and tear.
Reduced Downtime: With timed intervals for air cannon activation, material build-up is prevented, eliminating the need for shutdowns to address obstructions.
Schematic Diagram of Air Blaster Installation In Cement Pre-Heater
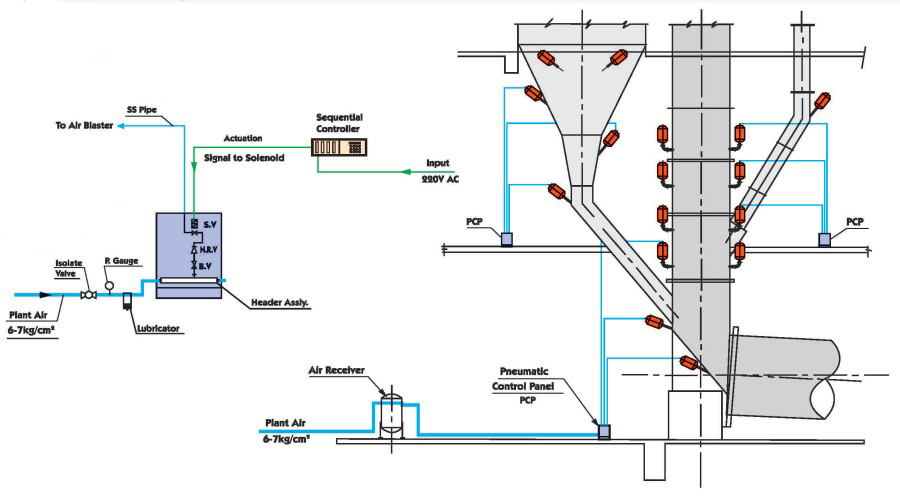
Concerns and Solutions
Material Build-Up
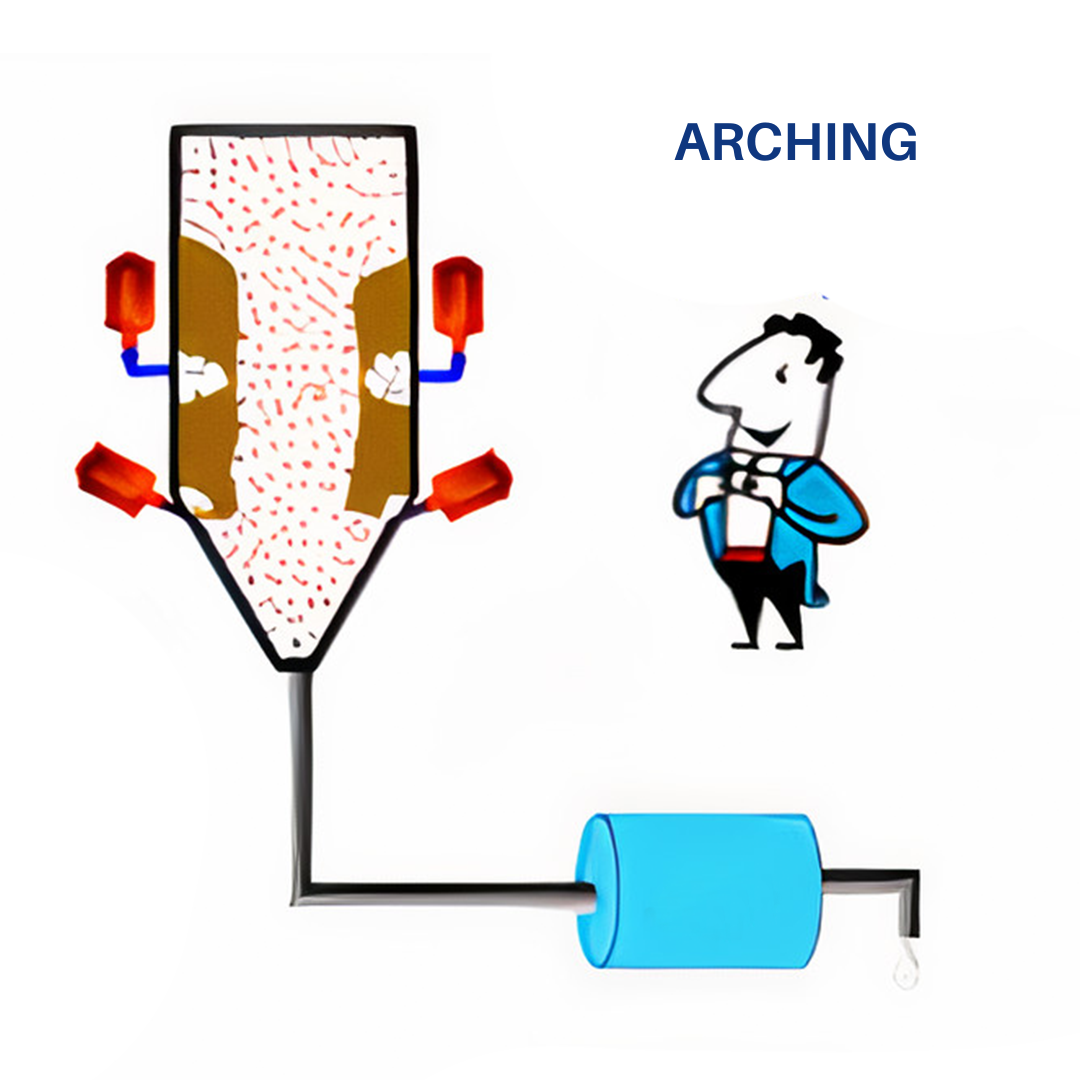
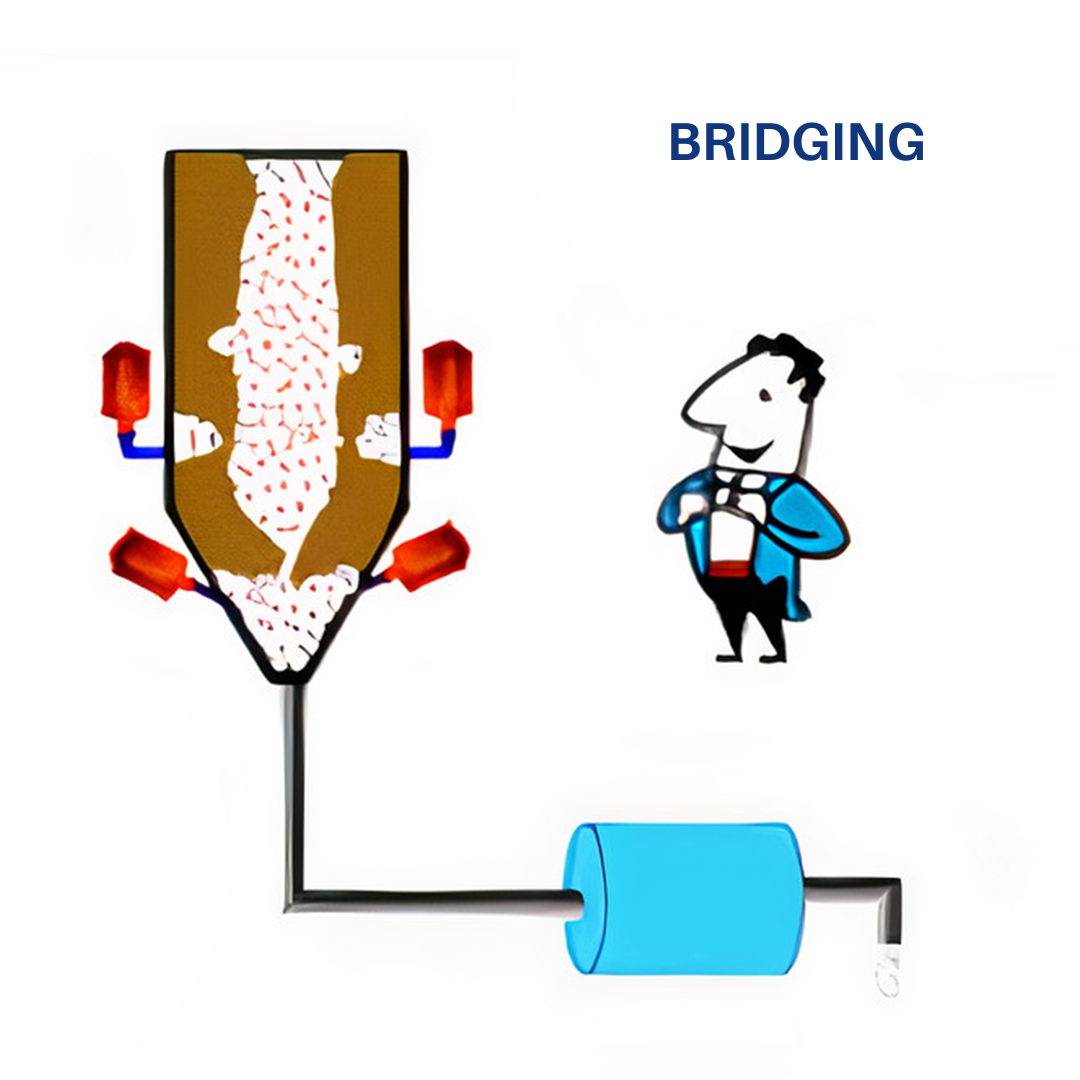
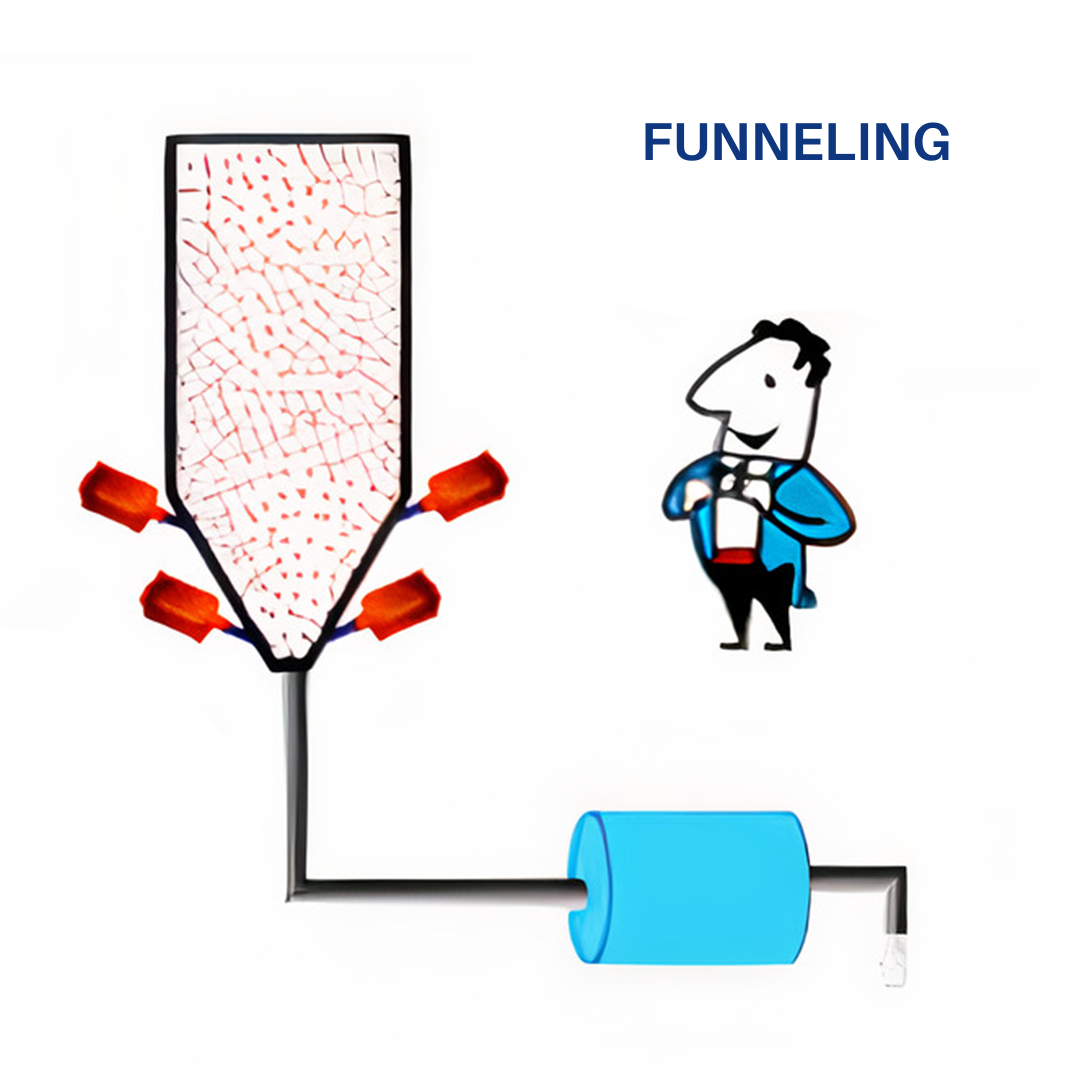
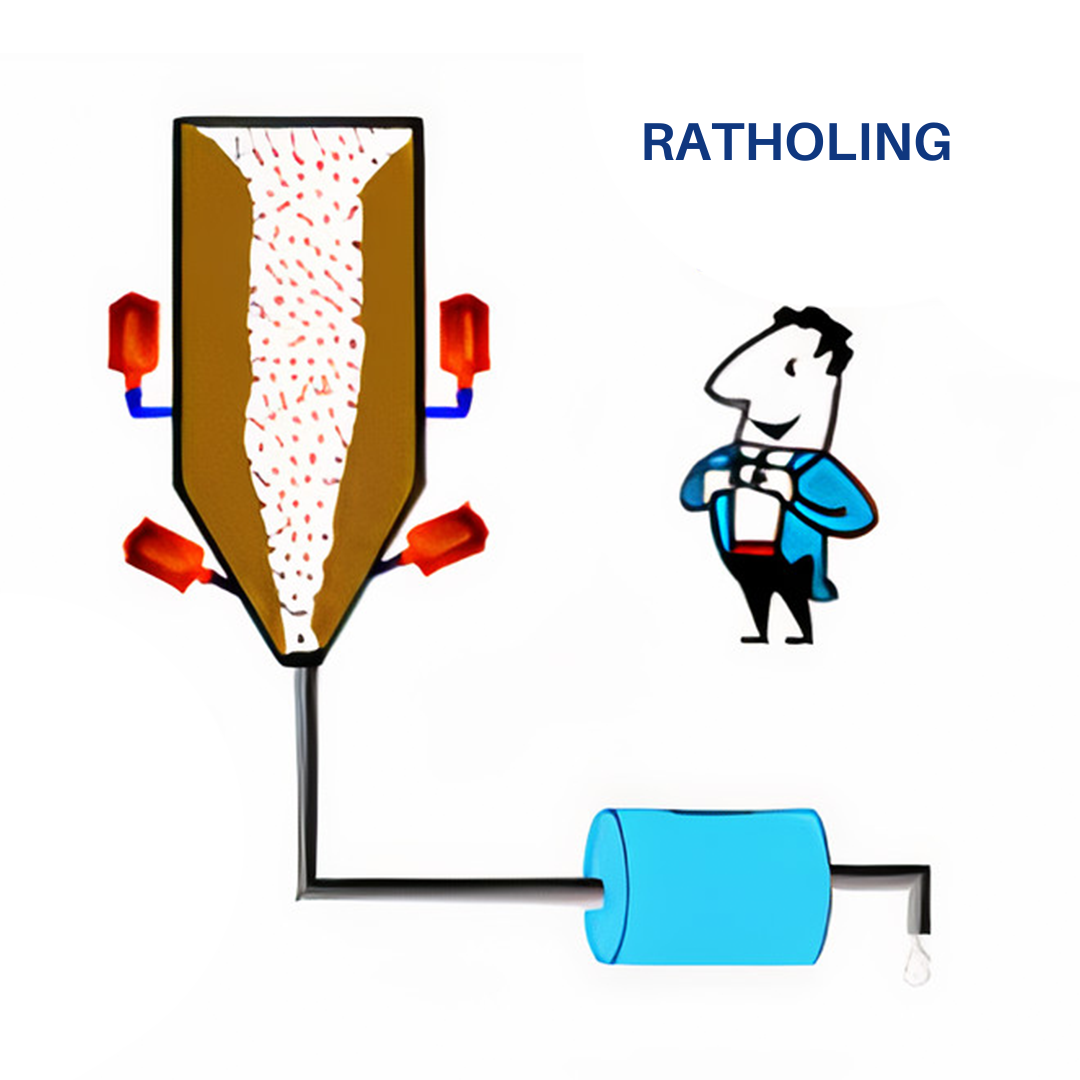
Air Blaster Demo
Air Blaster System Installation In Cement Plant
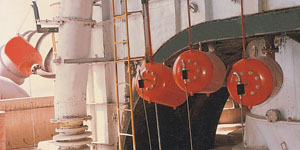
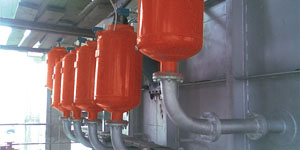
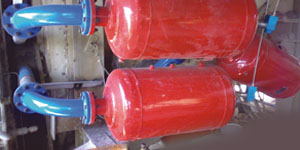
Technical Specifications Of Various Models
Model | Discharge | Tank Cap (Liters) | FAD at (5-7 kg/cm²) (In Liters) | Application |
---|---|---|---|---|
AB-05-04 | 50mm | 04 | 28 | Chutes, Feed Pipes, Section |
AB-05-08 | 50mm | 08 | 56 | Chutes, Feed Pipes, Section |
AB-05-12 | 50mm | 12 | 84 | Chutes, Feed Pipes, Section |
AB-05-020 | 50mm | 20 | 140 | Chutes, Small Section |
AB-10-050 | 100mm | 50 | 350 | Chutes, Feed Pipes |
AB-10-070 | 100mm | 70 | 490 | Chutes, Feed Pipes, Cylcone |
AB-10-100 | 100mm | 100 | 700 | Feed Pipe, Cyclone & Riser Duct |
AB-10-150 | 100mm | 150 | 1050 | Cyclone, Riser Duct, cooler, Hopper |
AB-10-300 | 100mm | 300 | 2100 | Cooler, Hoppers, Bunkers, Silos |
AB-15-050 | 150mm | 50 | 350 | Cooler, Hoppers, Bunkers, Silos |
AB-15-070 | 150mm | 70 | 490 | Cooler, Hoppers, Bunkers, Silos |
AB-15-100 | 150mm | 100 | 700 | Cooler, Hoppers, Bunkers, Silos |
AB-15-150 | 150mm | 150 | 1050 | Cooler, Hoppers, Bunkers, Silos |
AB-15-300 | 150mm | 300 | 2100 | Cooler, Hoppers, Bunkers, Silos |