Air blaster nozzles play a crucial role in the operation of air blasters. Air blasters are pneumatic devices used to clean and unclog bulk material handling equipment such as hoppers, silos, chutes, and bins. These devices use high-pressure air to create shockwaves that dislodge and remove accumulated material, preventing blockages and improving the flow of materials. The efficiency and effectiveness of an air blaster largely depend on the design and performance of its nozzles.
One of the key reasons why air blaster nozzles are important is their ability to direct the flow of compressed air. The nozzle design allows for precise and controlled targeting of the shockwaves to specific areas where material accumulation occurs. By directing the airflow directly at the problem areas, the nozzles maximize the impact force and ensure that the material is effectively dislodged. Without well-designed nozzles, the airflow may be dispersed and less concentrated, leading to less effective cleaning and increased energy consumption.
Another important aspect of air blaster nozzles is their durability and resistance to wear and tear. The high-pressure airflow generated by air blasters can be extremely abrasive, causing regular wear on the nozzles. Therefore, it is crucial to have durable and robust nozzles that can withstand the harsh operating conditions and maintain their performance over time. High-quality nozzles are typically made from materials such as hardened steel or ceramics, which can withstand the abrasive forces and provide long-lasting performance.
In conclusion, air blaster nozzles are essential components in the operation of air blasters. Investing in high-quality, well-designed nozzles is crucial for optimizing the performance and longevity of air blasters in industrial settings.
Nozzles options are available in both:
High Temperature Nozzles - SS 310/ HRCS - Grade - 9
Low Temperature Nozzles - MS Material
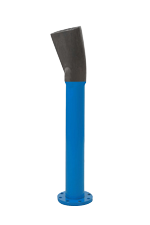
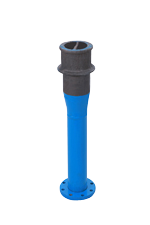
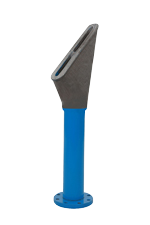
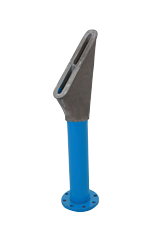
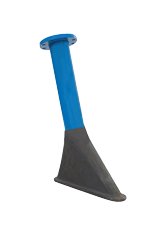
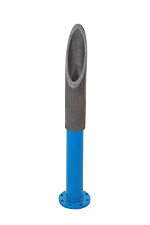
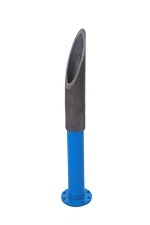
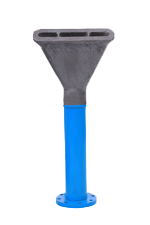
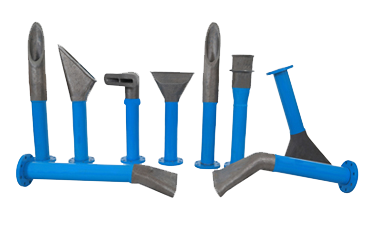